Customization Process
Our Customization Process is designed to bring your unique packaging vision to life, ensuring precision, functionality, and brand alignment every step of the way.
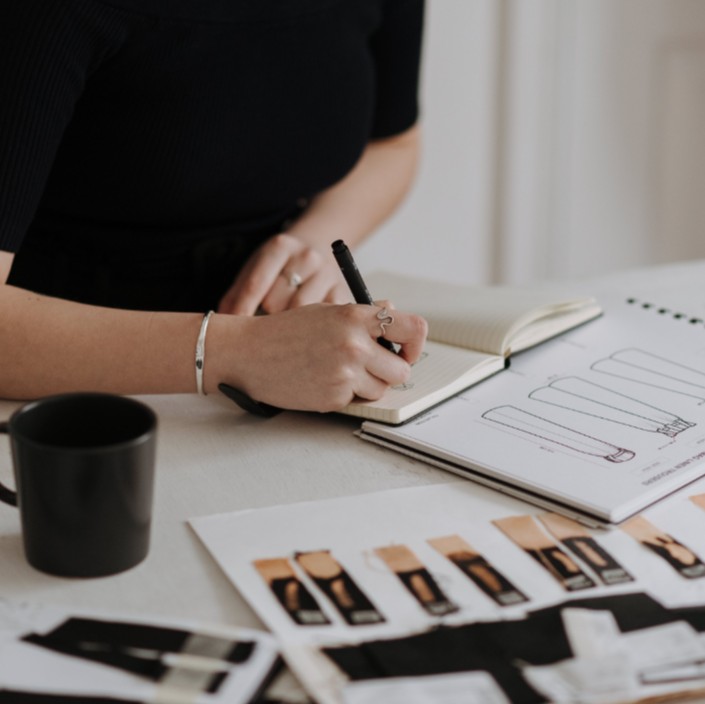
Design Concept
The journey begins with the conceptualization of your custom packaging, where we collaborate with customers to develop custom packaging solutions that meet industry standards and product requirements. From defining shape, size, and functionality to integrating specialized features like dispensing systems and closures, we ensure optimal performance and user experience. Branding elements such as embossing, debossing, and color-matching enhance shelf appeal, while our problem-solving approach addresses challenges like filling line compatibility, cost efficiency, and sustainability. Using advanced 3D modeling and prototyping, we create designs that are not only visually striking but also manufacturable and cost-effective.
Engineering & Design
At Empire Emco, we bridge the gap between concept and manufacturing by ensuring every custom mold is designed for precision and efficiency. Our engineering and design team works closely with customers to translate their packaging vision into detailed, manufacturable specifications. Using Computer-Aided Design (CAD) software, we create a digital representation of the mold, allowing for adjustments that optimize functionality, durability, and cost-effectiveness. This phase is critical for refining the design, ensuring compatibility with existing production lines, and addressing any potential manufacturing challenges before fabrication begins. By focusing on engineering excellence, we help our customers bring high-quality, innovative packaging solutions to market efficiently and effectively.
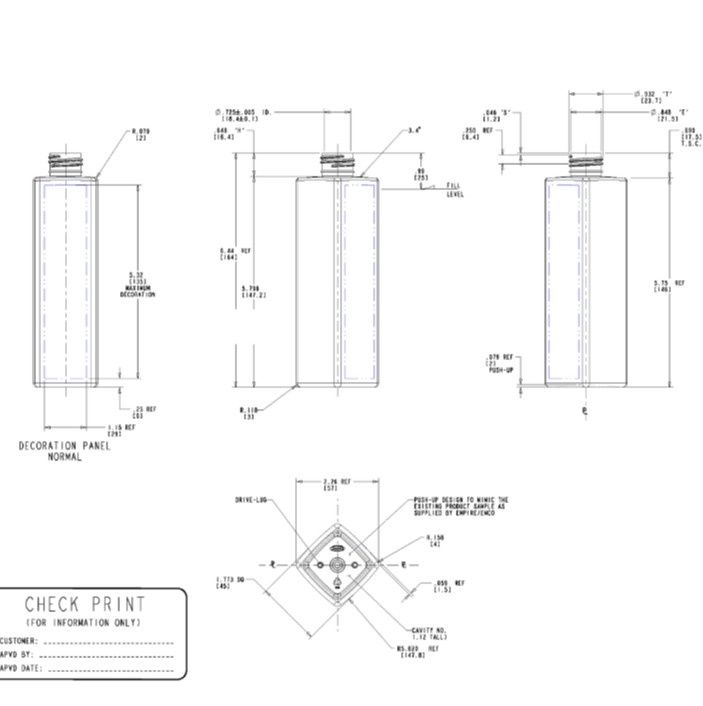
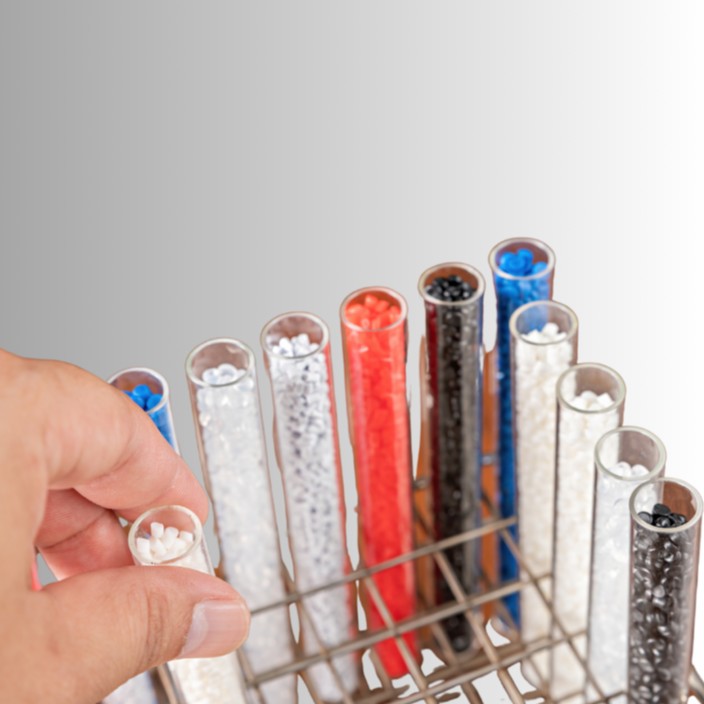
Material Selection
Selecting the right material is essential to achieving the best performance for your custom mold. As a packaging distributor, we help customers determine the most suitable material based on key factors such as the type of resin used in production, expected manufacturing volume, and durability requirements. Whether the mold needs to withstand high production runs or support sustainable packaging initiatives, we ensure that the material selection aligns with both functional and cost considerations, delivering a solution that enhances efficiency and product longevity.
Mold Fabrication
Once the design and material selection are finalized, the mold fabrication process begins. We partner with skilled tool and die makers who use high-precision machining techniques to craft molds from steel or aluminum, ensuring durability and accuracy. Precision is critical—even minor imperfections can impact production efficiency and product consistency. By leveraging advanced manufacturing technology, we ensure that the final mold replicates the desired packaging shape with exact detail, allowing for seamless integration into production lines and ensuring a high-quality, reliable end product.

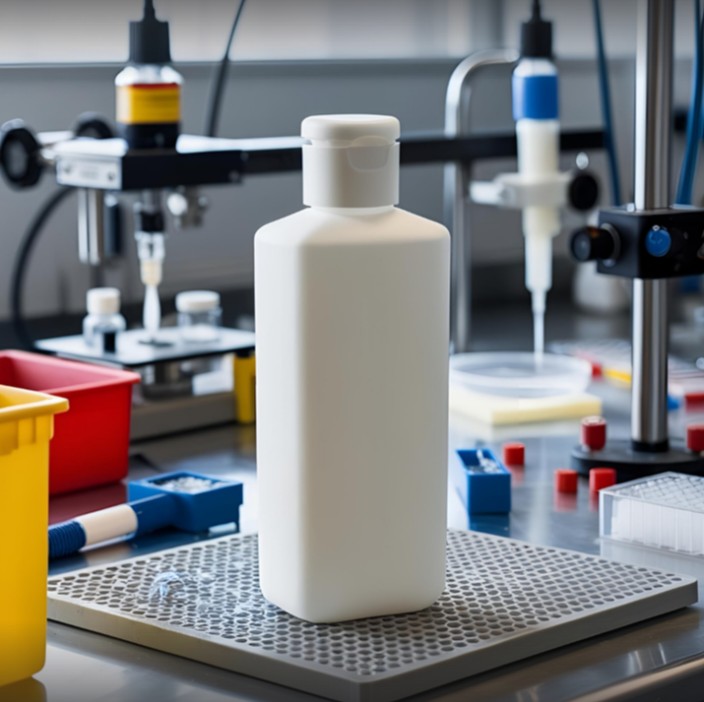
Testing & Prototyping
Before full-scale production, a prototype mold is created to evaluate functionality and ensure the packaging meets quality standards. This phase often involves producing a small batch of samples to test for structural integrity, consistency, and performance. Rigorous testing helps identify and resolve potential issues, such as imperfections or inconsistencies, ensuring the final mold produces high-quality, reliable packaging. By refining the design at this stage, we help our customers avoid costly adjustments later in the process.
Adjustments & Refinement
Following testing and prototyping, any necessary adjustments and refinements are made to the mold design to ensure optimal performance. This iterative process may involve multiple rounds of modifications and retesting to address any inconsistencies and enhance overall packaging quality. By fine-tuning the mold before full production, we ensure that the final product meets the highest standards of durability, functionality, and aesthetics, providing our customers with a reliable and efficient packaging solution.
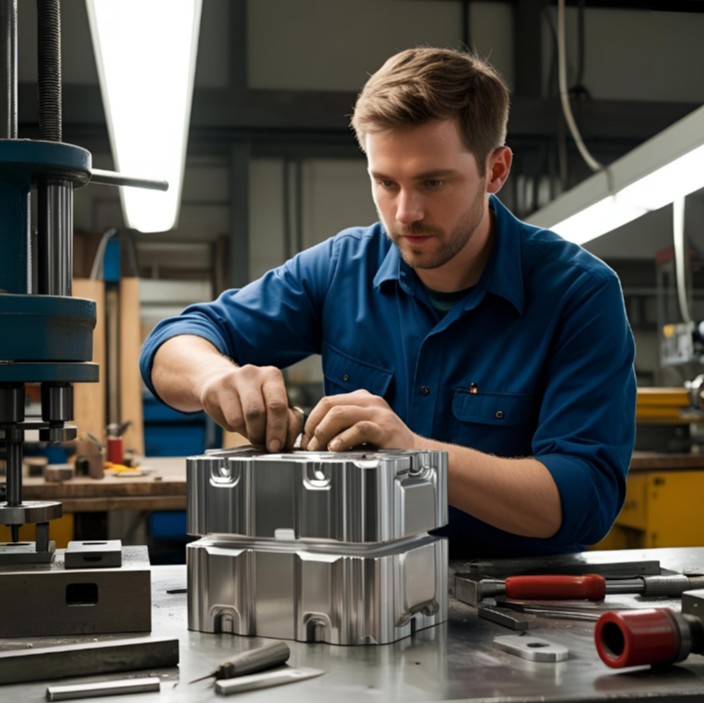
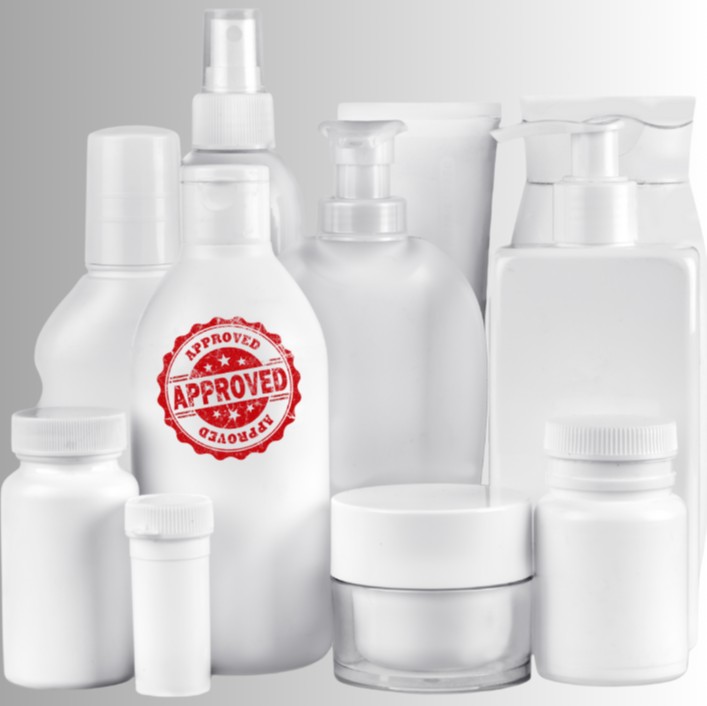
Final Approval
Once the prototype and mold design meet all required standards, the final mold is approved for mass production. This ensures that the mold is fully optimized for efficiency, durability, and seamless integration into the manufacturing process.
Production Setup
With approval secured, the mold is installed in either an injection molding or blow molding machine, depending on the chosen manufacturing process. Our team carefully sets production parameters such as temperature, pressure, and cycle time, ensuring they align with the properties of the selected plastic material for optimal performance and consistency.
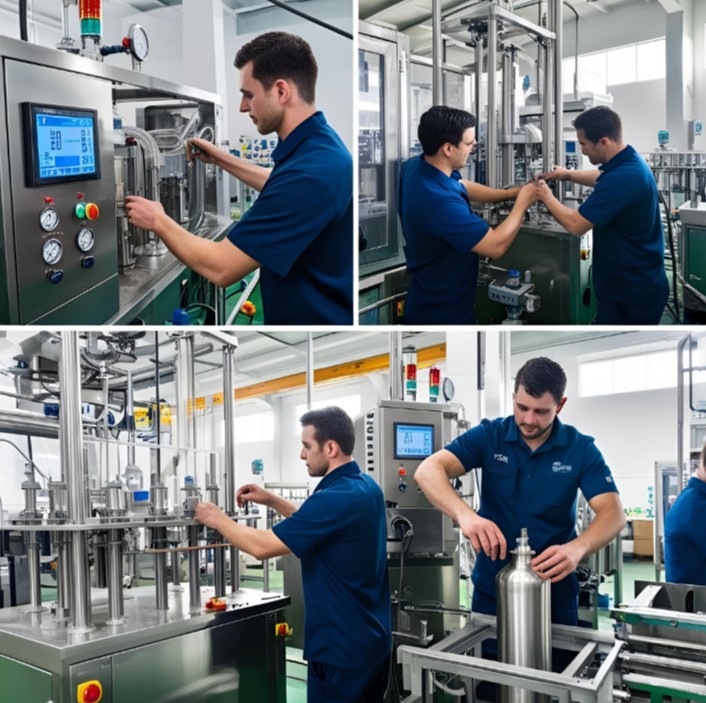
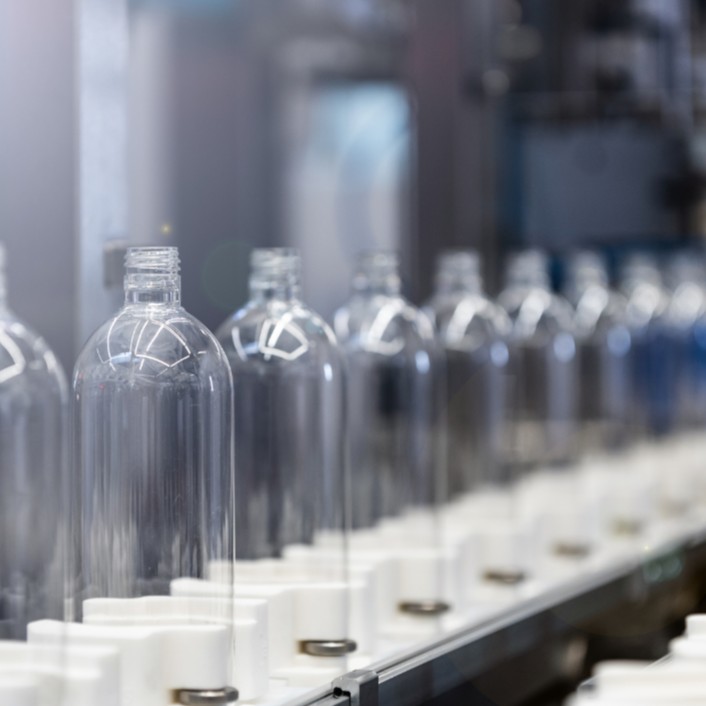
Mass Production
Mass production begins as plastic material is injected or blown into the mold cavities, forming the packaging components. Once the material has cooled and solidified, the finished units are ejected and prepared for downstream processing, such as trimming, decorating, or assembly if needed.
Quality Control
Throughout production, we implement rigorous quality control measures to ensure every packaging component meets the specified design, durability, and performance standards. By maintaining strict inspection protocols and testing procedures, we deliver high-quality, reliable packaging that meets the needs of our customers.
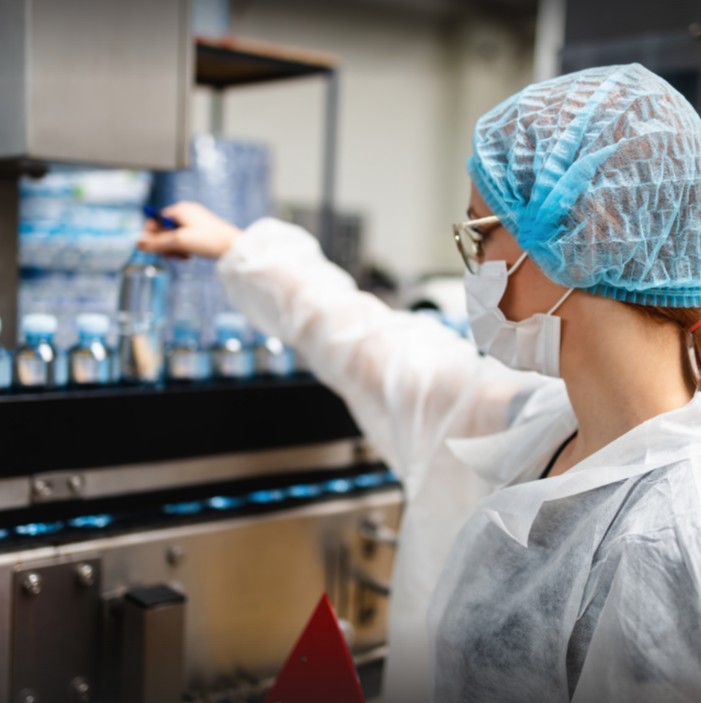
Collaboration & Process Flexibility
The custom mold process is a collaborative effort between designers, engineers, and manufacturing experts, ensuring that each packaging solution is developed with precision and efficiency. From concept to production, teamwork is essential to achieving a high-quality, functional, and cost-effective result. By leveraging industry expertise and advanced technology, we tailor each project to meet our customers’ unique packaging needs.
Dreaming of packaging, that’s distinctly yours?
Let's make it happen!
Make your brand unmistakable with our tailored design services. From distinct shapes to eye-catching colors, we bring your vision to life, crafting packaging that not only represents your brand but also grabs attention on the shelf. Let us help you create something truly one-of-a-kind.